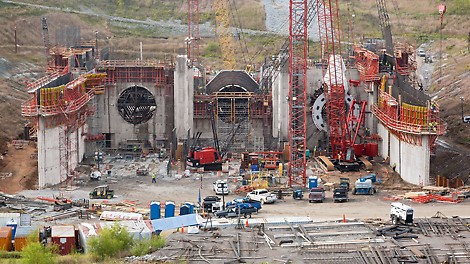
Smithland Hydroelectric Power Plant
Smithland, United States
Construction of a hydroelectric power plant with 3 horizontal bulb turbines and a total capacity of 72 MW
Reinforced concrete construction: 78 m long, 62 m wide, 32 m high
Massive component dimensions (slab thickness > 4.00 m)
Location
Main Application
Infrastructure
Project participants
Customer: CJ Mahan Construction Company, Grove City, OH
The Project
Impressions from the project process
The Smithland hydroelectric power plant is equipped with 3 turbines; due to the extremely tight construction schedule, all three tubes with their constantly changing cross-sections are being realized at the same time.
For the construction of the concrete tubes, PERI planned and assembled multi-curved formwork units. The final assembly of the formwork and shoring construction is carried out on site.
The fully assembled units comprising of formwork units and raised formwork are lifted by crane into the concreting position.
For constructing the power plant walls, the single-sided SCS climbing system is being used. The loads are transferred – without formwork ties – via the brackets in the climbing anchor of the previous concreting section.
The slab above the tubes is over 4.00 m thick and is constructed using several concreting steps. The high loads call for a long formwork utilization period, customized formwork units and heavy duty shoring towers.
The shoring inside the tubes, which later serve as turbine housing, consists of rentable system components taken from the VARIOKIT engineering construction kit. With the standardized system parts and construction compliant connecting means, supporting formwork can be cost effectively realized and easily adapted to suit the geometry of the structure.
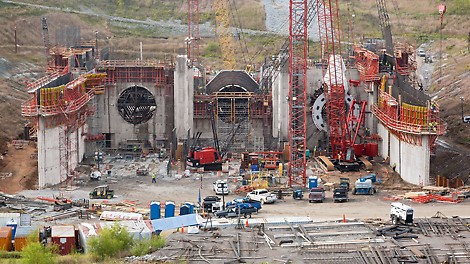
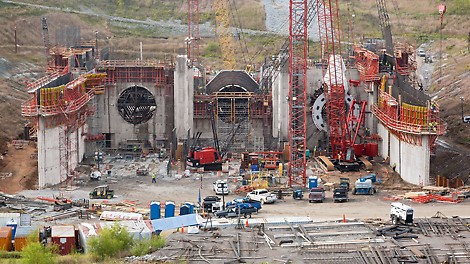
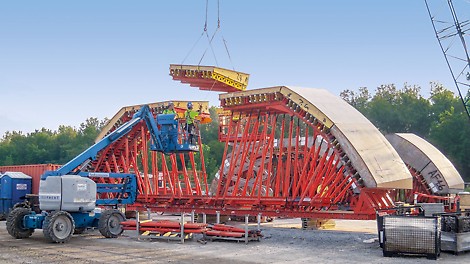
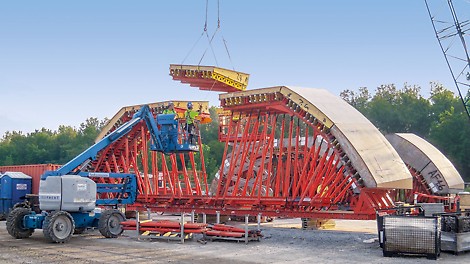
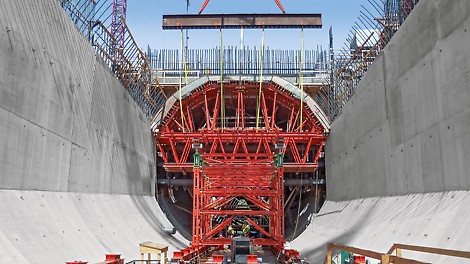
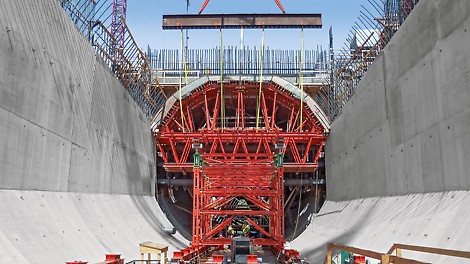
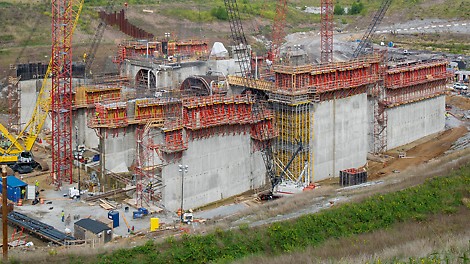
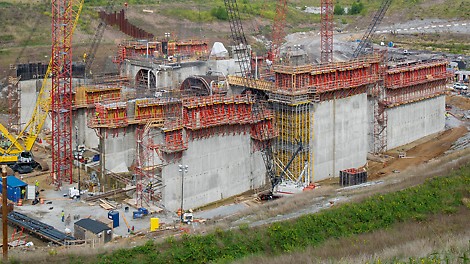
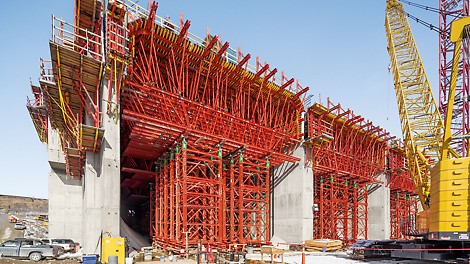
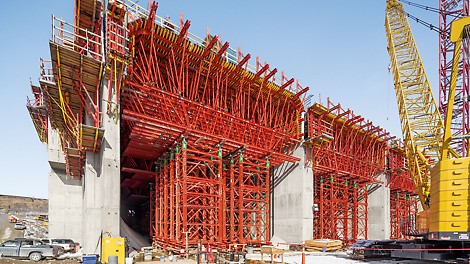
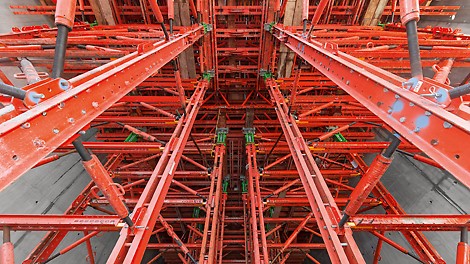
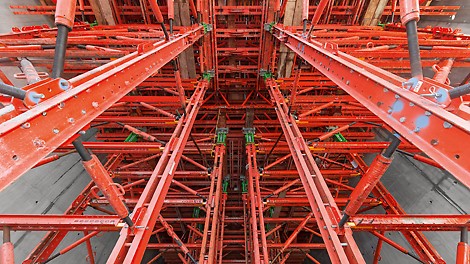
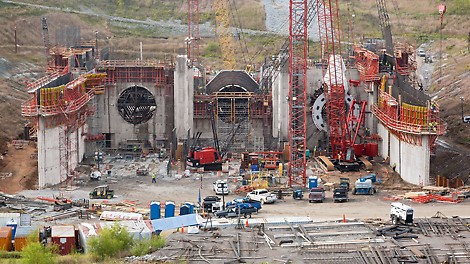
The Smithland hydroelectric power plant is equipped with 3 turbines; due to the extremely tight construction schedule, all three tubes with their constantly changing cross-sections are being realized at the same time.
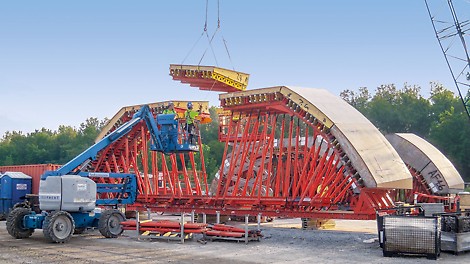
For the construction of the concrete tubes, PERI planned and assembled multi-curved formwork units. The final assembly of the formwork and shoring construction is carried out on site.
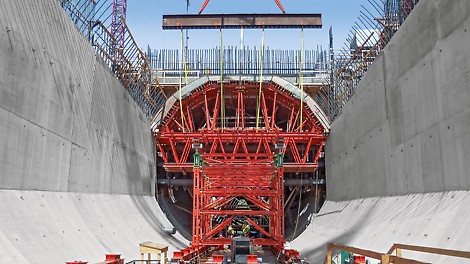
The fully assembled units comprising of formwork units and raised formwork are lifted by crane into the concreting position.
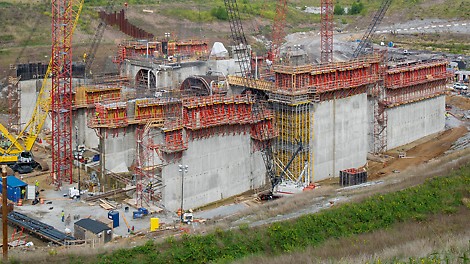
For constructing the power plant walls, the single-sided SCS climbing system is being used. The loads are transferred – without formwork ties – via the brackets in the climbing anchor of the previous concreting section.
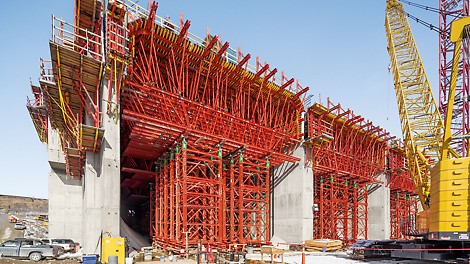
The slab above the tubes is over 4.00 m thick and is constructed using several concreting steps. The high loads call for a long formwork utilization period, customized formwork units and heavy duty shoring towers.
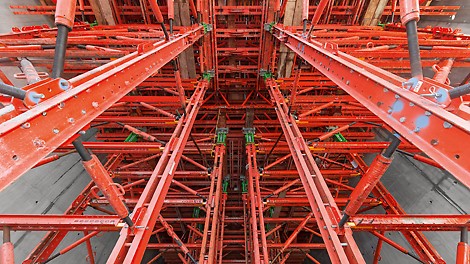
The shoring inside the tubes, which later serve as turbine housing, consists of rentable system components taken from the VARIOKIT engineering construction kit. With the standardized system parts and construction compliant connecting means, supporting formwork can be cost effectively realized and easily adapted to suit the geometry of the structure.
Project Information
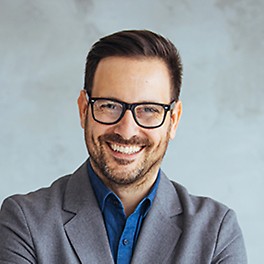
Call us on +971 (0) 4 326 2992 to discuss your requirements further.
Location
Smithland Hydroelectric Power Plant, Smithland, USA
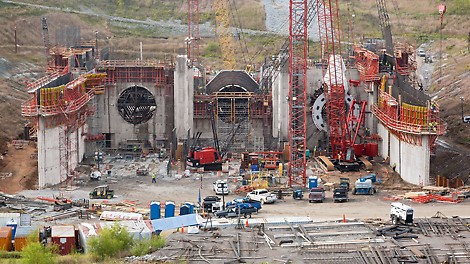
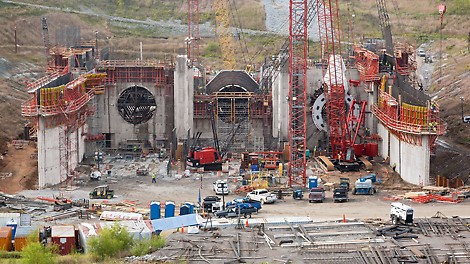