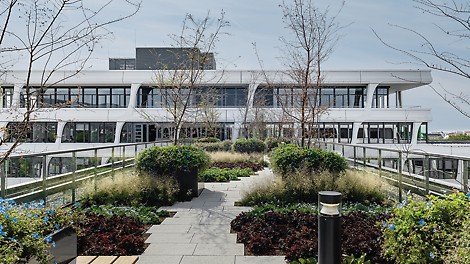
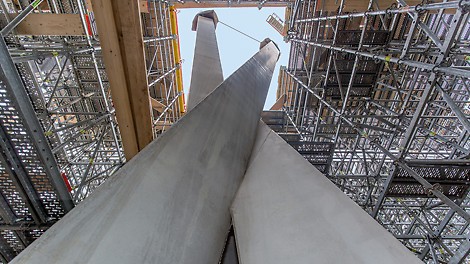
Download Press Release
The images in more detail
The new headquarters of the German building materials manufacturer HeidelbergCement clearly demonstrates what is possible with concrete. – and do so in the most impressive way possible. The results of using the highest quality architectural concrete class SB 4 and the finest white concrete are visible in the many architectural highlights. Spectacularly twisted tree-like supports, creatively patterned facade prefabricated concrete elements and sharp-edged beams in a radial pattern, make the new headquarters based in Heidelberg particularly eye-catching. A total of 31,500 m2 of concrete was used for the construction of the building, which consists of three interconnected parts of different heights and was opened in June 2020.
Successful cooperation in planning and execution
The architectural firm AS+P Albert Speer + Partner based in Frankfurt am Main was responsible for the project as general planner and carried out the design in cooperation with W+ Architektur- und Ingenieurgesellschaft mbH, with the latter providing the consulting office for the client’s project manager. The complex construction work was carried out by the building contractor Diringer & Scheidel.
PERI and the building materials manufacturer HeidelbergCement combined their architectural concrete expertise for the execution of this project. In doing so, existing limits were extended, and the wide range of possibilities offered by the building material concrete and the PERI product world were exploited. The architectural highlights of the project were successfully realised using special PERI formwork elements.
The view from outside
Even the bright, curved facade of the new headquarters impresses with its delicate filigree – despite the use of the solid building material concrete. The 11.75 m high facade supports in class SB 4 architectural concrete in white concrete are particularly striking. In order to construct the facade columns and their particularly smooth concrete surfaces in the highest quality, PERI timber girder formwork with multi-layer panels coated with melamine resin was used.
Individual planning and implementation of the tree-like supports
The focal point of the approximately 11 m high foyer of the HeidelbergCement headquarters is formed by two groups of tree-like supports, which from a structural point of view, serve as the root of the building. These tree-like supports in class SB 4 architectural concrete, each consist of three square cross-sections inclined towards each other, crossing approximately in the lower third. The special feature: in compliance with the architectural concrete quality required, only one panel joint is visible over the entire column height of around 11 m. An additional requirement was that no fastening screws, clamping holes and formlining joints were visible.
Due to the very high architectural concrete requirements, the statically required fresh concrete pressure of 200 kN/m² and the tough space limitations in the foyer, special formwork made of wood was not an option for implementing the tree-like supports. PERI therefore developed a highly complex 3D special formwork made of steel elements with an overall height of 150 mm. The basis for the three-dimensional design, which was carried out completely via the CAD systems PERI CAD and RHINO, was a 3D model of the tree-like supports, in which the later element separation points were already taken into account.
Sophisticated honeycomb structure
The supporting structure of the prepared special column formwork was a sophisticated honeycomb structure consisting of 63 CNC laser-cut individual parts. The individual parts were assembled as a plug-in system to avoid time-consuming welding. Each individual component had to be newly constructed and statically dimensioned. A total of around 12.7 t of steel was used to produce this formwork. 5-mm-thick steel formlining was then attached to the supporting structure to withstand the high level of fresh concrete pressure. At the point where the arms of the three tree-like supports cross, additional external ring constructions were attached to specifically counteract deformation of the steel.
Concrete pouring from below
In addition to the requirements for the colour and structure of the architectural concrete surface, another special feature was the pouring of the concrete: Unlike in most other cases, the concrete was not poured from above but from below. A concrete distribution system transported a total of 30 m3 of concrete simultaneously into three column sections and pressed the concrete upwards up to 11 m via three pump hoses in the formwork.
Real time determination of concrete pressure with PERI InSite Construction
Additional sensors of the PERI InSite Construction (ISC) Pressure Monitoring Set integrated into the formwork made it possible to measure the fresh concrete pressure in real time during the concreting process and to monitor it via the ISC Web Application on the mobile phone. The determined characteristic data for the formwork pressure provided a precise picture of the concreting process of the tree supports.
Use of special formwork for the feature wall
The walls of the foyer also stand out due to their architectural design. The so-called feature wall is characterised by its recessed, radial pattern, which consists of several prefabricated concrete elements that were retrofitted to the in-situ concrete wall. In addition to the highest architectural concrete quality of SB 4 standard and the white concrete used, an additional requirement was that no visible fastening points or tension holes should negatively impact the appearance. Furthermore, there are no visible vertical joints and a maximum of two visible horizontal joints at the height of the galleries. The butt joints were concealed by an overcut. In order to be able to realise the 8 cm thick prefabricated concrete elements (4 cm in the recesses), project-specific PERI special formwork was used.
Uneven cross vault in SB 4 grey concrete
Another challenge was encountered with the dome ceiling, which consists of an uneven cross vault with a circumferential edge upstand in SB 4 grey concrete. This was expected to be formed at a height of up to 7 m and a slab thickness of 25 cm. The desired result: a joint and butt-free appearance without visible fixing points on the formwork facing. The formwork solution that PERI developed for the implementation of the cross vault consisted of a total of 82 3D-designed architectural concrete timber formers. PERI designed and manufactured the timber formers especially for this project and delivered them pre-assembled to the construction site. There they were then mounted onto components of the PERI UP scaffold construction kit and were finally sealed. The PERI UP Weather Protection Roof ensured that work could be carried out regardless of the weather conditions so that the schedule could be adhered to regardless of the weather.
Diamond-shaped recesses in the casino
The casino on the ground floor of the new headquarters offers HeidelbergCement employees ample seating and a commercial kitchen. As one of the project highlights, this room features a special reinforced concrete ceiling with radial sharp-edged beams. These stand out in SB 4 white concrete from the underlying ceiling in SB 2 grey concrete mainly due to the striking shapes and colours. Here too, no visible fixing points of the formlining or bracing points of the beam formwork are visible.
For the slab, PERI special formwork developed especially for the project was used, which was later implemented with a total of 64 different diamond-shaped box outs pre-assembled in the factory. The load was transferred on four diamond-shaped supports with different cross-sections in the facade area. A VT 20 beam structure supplied by the contractor with a squared timber layer was opted for in the centre of the viewing panels. The pre-assembled viewing panels were fixed to a scaffold based on components of the PERI UP Scaffolding Kit. The special feature of the casino: First, the beams were created by simultaneously forming them from the outside to the inside with two pumps. Only then, after the beams had hardened, was the ceiling concreted.
Precise PERI support
A total of around 3,000 m2 of project-specific architectural concrete girder wall formwork was used during the project, most of which was pre-assembled in the factory and delivered to Heidelberg on schedule. The special challenges for the PERI engineers therefore included the intensive planning, the creation of individual special formwork solutions, as well as the support of the site personnel during the implementation of the complex geometries and shapes, and also the punctual provision of materials and coordination of the delivery dates.